活化處理是制備活性炭中重要的階段?;罨袃煞N方式:物理活化和化學(xué)活化。物理活化往往先要將原料炭化,然后在一定溫度下通入二氧化碳或水蒸汽,這種方式活化時間長,溫度高,耗能大?;瘜W(xué)活化是將炭化與活化同時進行的一種制備方式,簡化了操作,節(jié)省時間和能源,是目前應(yīng)用較多的活化處理方式。
Activation treatment is an important stage in the preparation of activated carbon. There are two ways of activation: physical activation and chemical activation. In physical activation, the raw material is often carbonized first, and then carbon dioxide or steam is introduced at a certain temperature. This method has long activation time, high temperature and high energy consumption. Chemical activation is a preparation method of carbonization and activation at the same time, which simplifies the operation and saves time and energy. It is a widely used activation treatment method at present.
氫氧化鉀活化法是從20世紀70年代發(fā)展起來的一種活化方法。氫氧化鉀作為活化劑,主要有抑制焦油生成,提高反應(yīng)收率,而且主要是利用氫氧化鉀、氧化鉀和碳酸鉀把原料中的部分碳浸蝕掉,經(jīng)過洗滌后生成多孔性的炭。
Potassium hydroxide activation method is an activation method developed from the 1970s. As an activator, potassium hydroxide mainly inhibits the formation of tar and improves the reaction yield. In addition, it mainly uses potassium hydroxide, potassium oxide and potassium carbonate to etch part of the carbon in the raw material and generate porous carbon after washing.
接下來通過以無煙煤為原料,KOH為化學(xué)活化劑進行活化過程中,通過熱分析實驗,獲得溫度與燒失率之間的關(guān)系,并探討KOH作為化學(xué)活化劑的活化過程。
Next, through the activation process with anthracite as raw material and KOH as chemical activator, the relationship between temperature and ignition loss rate is obtained through thermal analysis experiment, and the activation process of KOH as chemical activator is discussed.
用顎式破碎機將煤塊粗碎后,再用球磨機對顆粒煤進行細磨,將煤粉過200目篩后,得到原料1。稱取原料1煤粉145g,加入鹽酸(36.5%)10ml,氫氟酸(73%)10ml,高氯酸(37%)20ml,水50ml,攪拌均勻,室溫下浸泡24h。
After the coal is roughly crushed by jaw crusher, the granular coal is finely ground by ball mill, and the pulverized coal is sieved through 200 mesh to obtain raw material 1. Weigh 145g of raw material 1 pulverized coal, add 10ml of hydrochloric acid (36.5%), 10ml of hydrofluoric acid (73%), 20ml of perchloric acid (37%) and 50ml of water, stir evenly and soak at room temperature for 24h.
用抽濾裝置對上述原料洗滌,洗pH值為6后,置于電熱鼓風(fēng)千燥箱內(nèi)烘千水份,此為原料2。
Wash the above raw materials with a suction filtration device until the pH value is 6, and then place them in an electric blast drying box to dry thousands of water. This is raw material 2.
稱取烘干后煤粉10g,加入氫氧化鉀溶液(10%)10ml,攪拌成糊狀,放人表面皿,置于電熱鼓風(fēng)干燥箱中在105C保溫30min,此為原料3。
Weigh 10g of dried pulverized coal, add 10ml of potassium hydroxide solution (10%), stir it into a paste, put it in a watch glass, place it in an electric blast drying oven and keep it warm at 105C for 30min. This is raw material 3.
取原料1少許,以惰性氣體氮氣為保護氣,升溫速度為15C/min的情況下進行熱分析。
Take a little of raw material 1, take inert gas nitrogen as protective gas, and conduct thermal analysis at a heating rate of 15C / min.
取原料2少許,以氮氣為保護氣,升溫速度為15C/min的情況下進行熱分析。取原料3少許,以氮氣為保護氣,升溫速度為15C/min的情況下進行熱分析。
Take a little of raw material 2, take nitrogen as protective gas, and conduct thermal analysis when the heating rate is 15C / min. Take a small amount of raw material 3, take nitrogen as the protective gas, and conduct thermal analysis when the heating rate is 15C / min.
酸處理過的原料煤粉與未用酸處理過的原料煤粉的燒失率曲線有較大的差異:600C之前,酸處理過的原料煤粉僅有1.2%的燒失率,而酸處理過的原料煤粉燒失率已達28%,這主要原因是高氯酸浸泡煤粉后,已形成下面的分子模型:CooHz2Cho.49(HC104)1.4(H2O)3.8活化過程中,當(dāng)溫度升200C以上時,高氯酸浸蝕掉部分碳而使之失重。
The loss on ignition curve of acid treated raw coal powder is quite different from that of raw coal powder without acid treatment: before 600C, the loss on ignition rate of acid treated raw coal powder is only 1.2%, while the loss on ignition rate of acid treated raw coal powder has reached 28%, which is mainly due to the formation of the following molecular model after soaking coal powder in perchloric acid: coohz2cho 49 (hc104) 1.4 (H2O) 3.8 in the activation process, when the temperature rises above 200C, perchloric acid erodes part of the carbon and makes it lose weight.
從熱分析升溫350~550C之間時,樣品質(zhì)量基本保持不變,從DSC可以看到放熱峰。此時活化劑氫氧化鉀(熔點:360C)已為熔融狀,KOH開始分解:2KOH-K2O+H2O
When the temperature rises from thermal analysis to 350 ~ 550c, the sample quality basically remains unchanged, and the exothermic peak can be seen from DSC. At this time, the activator potassium hydroxide (melting point: 360C) has been molten, and KOH begins to decompose: 2koh-k2o + H2O
上述反應(yīng)發(fā)生的同時,生成的-OK基團取代原料中焦油某些H原子,原料開始脫氫,以氫氣的形式釋放出來,因此,KOH阻止煤焦油的揮發(fā)和促進了微晶層之間交聯(lián)網(wǎng)狀結(jié)構(gòu)的形成。
At the same time, the hydrogen atoms in the coal tar are replaced by KOH atoms to form a network structure, which prevents the formation of cross-linking between the above raw materials.
隨著溫度的繼續(xù)上升600C時,堿金屬化合物(如K2O和K2003)開始與碳發(fā)生反應(yīng),使得碳以氧化物形式釋放出來,同時有堿金屬鉀的形成,而鉀在石墨微晶平面之間的穿行,在沒有暴露的表面上產(chǎn)生刻蝕,從而增大微孔結(jié)構(gòu)和改變微晶體中芳香平面結(jié)構(gòu)及其電子分布情況,提高活性炭的性能。
As the temperature continues to rise to 600C, alkali metal compounds (such as K2O and k2003) begin to react with carbon, so that carbon is released in the form of oxide, and alkali metal potassium is formed. The passage of potassium between the planes of graphite microcrystals produces etching on the unexposed surface, so as to increase the microporous structure, change the aromatic plane structure and electronic distribution in the microcrystals, and improve the performance of activated carbon.
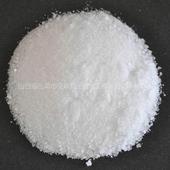
從熱流率曲線比較可以看出,在近700C時有一強吸收峰,該處可能為某活化反應(yīng)進行所吸熱而產(chǎn)生的變化,此時的DTG亦達到極值。因此,以KOH為活化劑制作活性炭時,在700C時保溫時間可能對活性炭吸附性能及孔徑結(jié)構(gòu)產(chǎn)生一定的影響。
From the comparison of heat flux curves, it can be seen that there is a strong absorption peak at nearly 700C, which may be the change caused by the heat absorption of an activation reaction, and the DTG also reaches the extreme value at this time. Therefore, when making activated carbon with KOH as activator, the holding time at 700C may have a certain impact on the adsorption performance and pore structure of activated carbon.
活化劑與原料煤粉混合物的實際燒失率與理論計算所得曲線(假設(shè)KOH與原料煤粉之間無作用)有較大的差異:
The actual loss on ignition rate of the mixture of activator and raw pulverized coal is quite different from the curve obtained by theoretical calculation (assuming that KOH has no effect on raw pulverized coal):
600C之后,由于K2O與K20O3與碳之間發(fā)生化學(xué)反應(yīng)導(dǎo)致實際重量損失率比計算大得多,其原因是堿金屬氧化物(如K2O與K2CO3)開始與碳發(fā)生反應(yīng),使得碳以氧化物形式釋放出來。
After 600C, the actual weight loss rate is much larger than calculated due to the chemical reaction between K2O, k20o3 and carbon. The reason is that alkali metal oxides (such as K2O and K2CO3) begin to react with carbon, so that carbon is released in the form of oxide.
當(dāng)溫度大于800C時,一方面會導(dǎo)致燒失率增大,產(chǎn)品得率低,另-方面可能過多的碳燒失后導(dǎo)致微孔結(jié)構(gòu)坍塌,使得活性炭孔徑分布不理想,所以適宜的活化溫度在750~800C之間。根據(jù)KOH的活化特性,以不同的活化工藝,可以研制出性能優(yōu)良的活性炭樣品。
When the temperature is greater than 800C, on the one hand, it will increase the loss on ignition rate and low product yield. On the other hand, it may lead to the collapse of microporous structure after excessive carbon loss on ignition, resulting in the unsatisfactory pore size distribution of activated carbon. Therefore, the appropriate activation temperature is between 750 ~ 800C. According to the activation characteristics of KOH, activated carbon samples with excellent properties can be developed by different activation processes.
通過實驗講解氫氧化鉀的活化處理的相關(guān)內(nèi)容便是這樣了,當(dāng)然在實驗過程中還是要做好保護措施,人身很重要,更多內(nèi)容就來網(wǎng)站
www.hkjzshop.com咨詢吧!
This is how to explain the activation treatment of potassium hydroxide through experiments. Of course, protective measures should be taken during the experiment. Personal safety is very important. For more information, please visit www.hkjzshop.com Com consultation!